Different Types of Quality Inspections When Manufacturing a Product
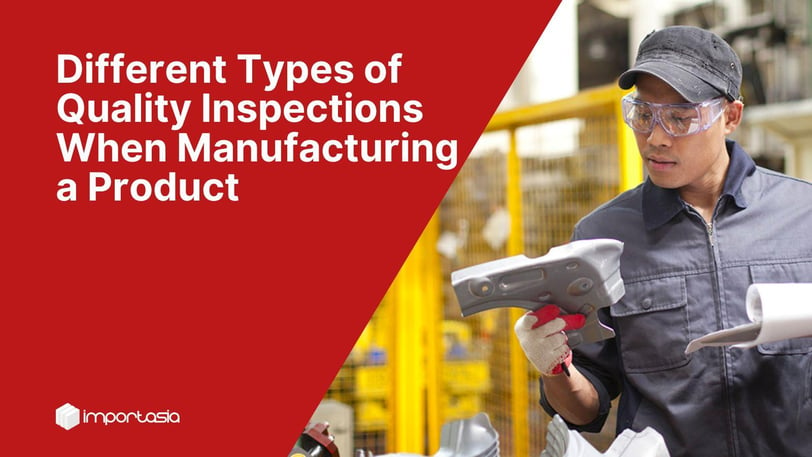
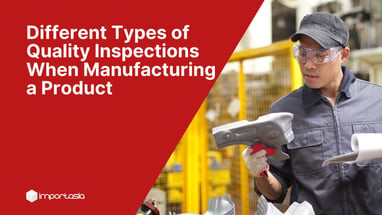
Quality inspection is a critical aspect of any manufacturing process, and it plays a vital role in ensuring that products meet the required quality standards. There are four types of quality inspection, each serving a specific purpose in the manufacturing process. These types of quality inspection include pre-production inspection, during production inspection, pre-shipment inspection, and container loading inspections.
Pre-Production Inspection (PPI)
The first type of quality inspection is pre-production inspection. This type of inspection takes place before the manufacturing process begins, and its primary goal is to ensure that all necessary raw materials are available and meet the required quality standards. Pre-production inspection also ensures that the manufacturing process runs smoothly without any unnecessary interruptions or delays. Manufacturers should conduct pre-production inspections to identify any potential quality issues with raw materials, production equipment, or the manufacturing process itself. This will help manufacturers address any issues early and prevent any potential defects or issues with the final product.
A Pre-Production Inspection (PPI) can be particularly advantageous when working with a new supplier, especially for large contracts with critical delivery dates. Conducting a PPI can minimize or eliminate communication gaps between you and your supplier regarding production timelines, shipping schedules, and quality requirements.
The following are some of the key areas that are typically covered in pre-production inspections:
Raw Materials
One of the critical areas that pre-production inspection focuses on is the quality of the raw materials that will be used in the manufacturing process. Inspectors will check the raw materials to ensure that they meet the required quality standards and specifications. They will also verify that the materials are free from any defects or damage that could affect the quality of the final product.
Production Equipment
Another essential area that pre-production inspection covers is the production equipment. Inspectors will check the equipment to ensure that it is in good working condition and meets the required safety standards. They will also ensure that the equipment is calibrated correctly and that it is suitable for the specific manufacturing process.
Production Process
Pre-production inspection also involves reviewing the production process itself. Inspectors will check that the process is well-documented, and all necessary controls are in place. They will also verify that the process is capable of producing products that meet the required quality standards.
Facilities
Inspectors will also check the facilities where the manufacturing process will take place. They will ensure that the facilities meet the required safety and hygiene standards and that they are suitable for the specific manufacturing process. Inspectors will also check that the facilities are equipped with the necessary tools and equipment to support the production process.
Documentation
Finally, pre-production inspection will cover the documentation required for the production process. Inspectors will check that all necessary documentation is complete, accurate, and up to date. This includes items such as work instructions, inspection records, and quality control plans.
During Production Inspection (DPI)
As the name suggests, during production inspection takes place during the manufacturing process. This approach is especially beneficial for items that are produced continuously and have stringent specifications, or when quality problems have been identified before production during a previous PPI.
The primary objective of this inspection is to monitor the production process and ensure that everything is on track. During production inspection helps manufacturers identify any potential issues early on in the production process, reducing the cost and time required to address them. It also ensures that the product quality meets the required standards, specifications, and customer expectations.
The main objective of DPI is to identify any deviations from the agreed-upon quality standards or product specifications and to address them before production continues. This inspection can help manufacturers ensure that they meet customer expectations, comply with regulatory requirements, and avoid costly production delays.
A DPI can involve a range of inspection activities, including visual inspection, sampling, testing, and analysis. Depending on the product being manufactured, the inspection can focus on different aspects of the production process, such as the raw materials used, production equipment, production processes, and finished products.
During a DPI, inspectors may look for defects, damages, or inconsistencies in the product's design, manufacturing process, and quality standards. They may also check for safety and regulatory compliance, such as the use of proper labeling, packaging, and handling of hazardous materials.
The frequency of DPIs can vary depending on the manufacturing process, the product being produced, and the customer's quality requirements. However, in general, DPIs should be conducted regularly throughout the production process to ensure that any problems are identified early and addressed before they escalate.
In conclusion, DPI is an integral part of quality control and is essential for ensuring that production runs smoothly and that the final product meets the required quality standards. By catching any potential issues early in the production process, manufacturers can save time and money and avoid costly production delays. Regular DPIs should be conducted throughout the production process to ensure that the final product meets customer expectations and complies with relevant regulations.
Pre-Shipment Inspection (PSI)
Pre-shipment inspections (PSI) play a crucial role in ensuring the quality of goods before they are shipped, making it an essential step in the quality control process. The primary objective of PSI is to ensure that the production of goods adheres to the buyer's specifications. The inspection process is usually carried out on finished products when at least 80% of the order has been packed for shipping. During the inspection, a set of random samples are chosen and inspected for defects against relevant standards and procedures. By doing this, the inspection team can identify any defects or issues in the finished products before they are shipped to the buyer.
During a PSI, inspectors usually examine a sample of finished products randomly selected from the production batch. Inspectors then evaluate the products against agreed-upon quality standards, product specifications, and other relevant requirements. They may use various testing methods, including visual inspections, measurements, and performance tests, to check for product quality and compliance.
The PSI process focuses on the following critical areas:
Quality control
Inspectors check for defects, damage, or inconsistencies in the product's design, production process, and quality standards. They may also verify that the product meets customer expectations in terms of functionality, performance, and appearance.
Packaging and labeling
Inspectors check that the product is packaged correctly and labeled appropriately. They may verify that the packaging materials are suitable for the product, that the labels are accurate and comply with relevant regulations, and that the product is adequately protected during transportation.
Regulatory compliance
Inspectors verify that the product complies with relevant regulatory requirements, such as safety, environmental, or health regulations.
The frequency of PSIs may vary depending on the product being produced, the customer's quality requirements, and the manufacturing process's complexity. However, it is generally recommended that PSIs be conducted regularly to ensure that the final product meets the required quality standards and specifications.
PSIs are an essential quality control process that ensures that the final product meets the required quality standards and specifications and is free from defects. By conducting regular PSIs, manufacturers can ensure that their products meet customer expectations, comply with relevant regulations, and avoid costly returns or product recalls. Whether conducted internally or by third-party inspection companies, PSIs should be an integral part of any manufacturer's quality control process.
Container Loading Supervision (LS)
The inspection aims to assess the condition of the shipping container and ensure that all the products are loaded safely and correctly. It involves verifying the product information, quantities, and compliance with packaging requirements.
Container loading inspections are essential steps in the quality control process to ensure the safety and protection of goods during transportation. This inspection process is especially critical for goods that are shipped over long distances or transported via multiple modes of transportation.
The container loading inspection is the final quality inspection in the process, and it occurs just before the products are loaded onto the shipping container. The inspection aims to ensure that the products are loaded safely and correctly and that they are protected during transportation.
The first step in this inspection process is to check the container's condition to ensure that it is clean and free from any damages or defects that could potentially affect the products' safety. The inspection team will also verify that the container is suitable for the type of products being shipped and that it has the required temperature and humidity controls, if necessary.
The inspection team will then examine the products to ensure that they are packaged correctly and that they fit securely in the container. The products should be arranged in such a way that they are protected from damage during transportation, and there should be enough space between them to prevent them from shifting or moving during transit.
During the inspection, the team will also check that the products are labeled correctly and that all necessary documentation, including the shipping invoice, packing list, and customs documents, are present and accurate. This documentation is essential for customs clearance and ensuring that the products reach their final destination without any delays or complications.
After the inspection is complete, the team will provide a report that details any issues or concerns identified during the inspection. This report will be shared with the shipping company and the buyer, and any necessary corrective actions will be taken to ensure that the products are shipped safely and in compliance with relevant regulations
Conclusion
In summary, quality inspection is an essential aspect of any manufacturing process. Manufacturers must conduct all four types of quality inspections to ensure that their products meet the required quality standards, specifications, and customer expectations. Pre-production inspection ensures that all necessary raw materials are available and meet the required quality standards. During production inspection monitors the production process and identifies any potential issues early. Pre-shipment inspection ensures that the final product meets the required quality standards, specifications, and customer expectations. Container loading inspections ensure that the products are loaded safely and correctly and are secure during transportation. Conducting all four types of quality inspections can help manufacturers improve product quality, reduce production costs, and increase customer satisfaction.